Highway maintenance - Projects & progress
On this page:
Projects & progress
Source: WSDOT Maintenance and Operations Office
Performance analysis
2024
WSDOT Maintenance faces challenges from mounting third-party damages
WSDOT Maintenance faces significant challenges due to financial constraints and rising operational demands. The need to maintain Washington's transportation infrastructure has outstripped the available funding, which was worsened by a 33% increase in third-party damages costing $22.5 million by June 2024.
From 2015 to 2024, tort claims related to potholes increased by 322.7%. In the last five years, claims surged from 124 to 634, a 411.3% increase in 2024. Deferred roadway maintenance due to insufficient funding prioritization at WSDOT can lead to deteriorating road conditions, increasing the risk of vehicle damage and accidents. As a result, the likelihood of tort claims against the agency rises, as motorists may seek compensation for injuries or damages caused by hazards such as potholes, failed pavement, or poor roadway markings.
To absorb these costs, WSDOT had to cut back on high-material-usage activities like striping, pavement repair and vegetation spraying, resulting in reduced roadway visibility and slower response times. Measures such as overtime, travel restrictions and a hiring freeze have also been implemented to decrease expenses. Despite these efforts, inadequate funding is exacerbating infrastructure deterioration, leading to the need for emergency repairs and increasing potential safety risks.
As a temporary solution in instances where WSDOT is unable to repair roadways, "Rough Road" signage has been placed in 55 locations and continues to increase. This has been done to alert drivers to issues like potholes and uneven surfaces while highlighting a growing backlog of maintenance needs. It is important to understand the maintenance program has extended the life of transportation assets although service level reductions are expected to continue until adequate funding is provided for both the Maintenance Operations and the Preservation programs. The difficulty falls in where direction for funding will land, rather than the direction the WSDOT would prioritize.
Keller Ferry disruptions create challenges for WSDOT's Maintenance Operations program
The Keller Ferry is a single-vessel, on-demand service operated by WSDOT and maintained by maintenance operations. The M/V Sanpoil crosses Lake Roosevelt and links rural communities in Lincoln and Ferry counties along State Route 21, providing critical local mobility and access to goods and commerce. Despite its lower traffic volume, it is essential, as no alternative crossings are available for miles. Disruptions to this service add significant travel time for residents, services, and emergency vehicles. It operates on-demand, 6:00 a.m. to midnight, seven days per week.
In 2024, the Keller Ferry faced multiple disruptions, which significantly strained WSDOT's Maintenance Operations Program. Repeated mechanical failures required emergency repairs, redirecting crews and resources from scheduled maintenance across the state. The Keller Ferry's operational challenges have delayed critical tasks such as road repairs and asset condition assessments and led to an uneven allocation of resources, with rural and underserved areas potentially experiencing longer delays in service delivery. The heightened focus on the ferry's immediate needs underscored the program's vulnerability to unexpected events, illustrating the need for flexibility in planning and staffing.
The frequency of the interruptions raised concerns about the ferry's reliability and underscored the challenges of maintaining essential infrastructure. Keller Ferry had problems with frozen pipes, resulting in the service being shut down from January 10-25, 2024. Operations were affected in summer by the Swawilla Fire, which necessitated temporary closure to support evacuation efforts and ensure public safety. It was removed from service again in late November due to steering system failures. Although repairs allowed it to resume operations briefly, similar issues reoccurred on November 27, leading to another suspension of service. After intensive repair efforts, service was restored on December 14.
The unplanned repairs increased operational costs and placed pressure on the budget, potentially diverting funds from preventive maintenance and upgrades. The reliability issues have also frustrated local communities, highlighting the need for a balance between immediate repair needs and long-term infrastructure planning to ensure a dependable transportation network in Washington state.
2023
WSDOT 2023 Highway Maintenance Survey Overview
The 2023 Highway Maintenance Survey was conducted in February 2023 when a consultant working for WSDOT reached out to 900 highway users. This statewide survey is conducted every seven years and is used to gauge customer satisfaction with state highway maintenance activities and compare results to previous iterations of the highway maintenance survey. Quotas were set by age and gender, number of miles driven per week, and region of the state to ensure a sample that reflects different state highway users across Washington.
Satisfaction for individual maintenance categories remained at or near historical averages for most maintenance categories despite a drop in general satisfaction from 2017 to 2023. Road surface maintenance is both the most important maintenance category and the category residents most want to see improved. When asked if they are generally satisfied with the maintenance of state highways, 57% said "yes" in 2023 compared to a 75% average across previous surveys. However, for individual categories the lowest level of satisfaction is 61% (litter and trash removal) and the average across all categories is 77%.
The WSDOT Maintenance Accountability Process results from the past few years indicate a downward trend in the condition of the assets WSDOT is tasked to maintain. This demonstrates the need to invest in system preservation and maintenance to restore WSDOT's assets to a level that satisfies the needs of the traveling public while considering the lowest life cycle cost of these assets. Investment in strategic preservation funding would allow WSDOT to shift its focus back to a more pro-active approach to maintaining assets, which would be more cost-effective and efficient.
2022
WSDOT faces a shortage of maintenance employees
It is estimated between 2021 and 2031, 1.7 million people per year will leave their jobs in the transportation infrastructure sector, according to the Bureau of Labor Statistics. Nationwide, there has been an increasing demand for drivers with Commercial Driver s Licenses (CDL) and mechanics. For states this has resulted in shortages due to:
- Fewer people are becoming CDL drivers, which translates into fewer people available to fill these positions
- Higher private salaries and signing bonuses, which make states less competitive
- An aging workforce starting to retire
To keep up with the ever-growing demand for qualified employees, WSDOT is hiring more people without their CDLs and providing the training to obtain them. WSDOT has provided CDL training to 129 individuals and has another 22 waiting for a spot in a commercial school or to start an in-house training.
WSDOT Maintenance offers an in-house workforce development program in many different areas to ensure that Washingtonians have a safe, sustainable, and integrated multimodal system.
The different tiers of in-house training consist of entry-level, technical, and leadership-focused curriculums. In 2021-2022, WSDOT started a "High School to Highways program," which directly led to 23 people being hired.
WSDOT's Low Voltage Auto Start system saves time and money
Maintenance employees are encouraged to share and implement ideas or solutions to everyday problems and issues that crews encounter through the department's annual Innovations Program. Many teams across the state bring forward new ideas to save time and resources while increasing work zone and personnel safety.
The Low Voltage Auto Start system took first place at the WSDOT Innovations Challenge in 2022. WSDOT vehicles equipped with beacon lights or message signs need to be left in work zones or near hazard locations for prolonged periods. The system allows the operator to leave a vehicle unattended while it powers devices that communicate information to the traveling public.
When activated, the system battery voltage is monitored, and when it drops to 11.5 volts, the vehicle will start up and run for a predetermined time period to properly recharge the batteries. Once the batteries are charged, the system then shuts off the vehicle. The system will continue to operate in this manner until it is deactivated. It includes safety features for technicians that prevent activation if the hood is open or the doors are unlocked, the engine shuts off when the system is activated and the brake pedal is pressed to reduce the likelihood of the vehicle being stolen.
Benefits of the Low Voltage Auto Start system include:
- A 70% reduction in idle time
- Reduced fuel consumption
- Smaller carbon footprint
- Less maintenance on heavy truck emission components
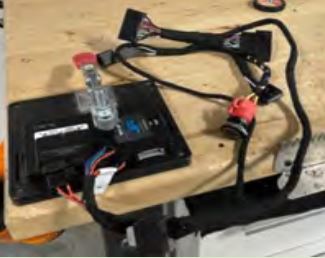
2021
WSDOT innovations help clear snowy roads
WSDOT—through a partnership with the Transportation Equipment Fund, Eastern Region Maintenance and Henke Manufacturing—was able to develop a plow that clears the traveled lanes and the shoulder on secondary highways with a single pass. The "breakaway" design for a 3-foot extension, which brings the total plow width to 15 feet, was constructed and piloted in WSDOT's Eastern Region during the 2020-2021 winter.
The extendable plow was used on a modified truck, but it can be installed on any truck and used as a standard plow if needed.
In the past, WSDOT Maintenance would install a second "wing plow" on the side of the vehicle to reach shoulders. Doing so added weight to one side of the vehicle and also required more controllers to operate the two, separate plows.
Designed with safety in mind, the new extendable plow is highly visible from inside the cab. With only one blade to monitor, it eliminates the problems associated with using two blades. The extended plows can easily be adjusted when the truck is approaching guardrail or bridges and minimize the time it takes to transition the trucks from season to season.
2020
COVID-19 impacts maintenance activities
The COVID-19 pandemic significantly affected all WSDOT maintenance activities and operations. Due to the Governor's Stay Home, Stay Healthy order starting in March 2020, maintenance crews had to pause planned work activities and shift to items including online training in a telework capacity. Missing the key work window of early spring/summer exacerbated the backlog of needed maintenance activities. Once safety procedures were developed to return to work, crews returned slowly to ensure everyone's safety and to adhere to new guidelines.
The ongoing safety guidelines and personal protective equipment are vital, but also increase the time it takes crews to complete certain jobs. Emergency crews continued to respond during the Stay Home order, and often had to be creative in crewing and equipment to keep themselves and others safe.
Powered Air Purifying Respirators, normally used for grinding or cutting concrete on bridge desks or asbestos inspections, were used by general maintenance crews who could not stay six feet away from each other while completing tasks. The battery-powered devices provide clean air to workers and a higher degree of air filtration than a typical N95 mask.
Throughout the pandemic, frontline maintenance crews did additional cleaning and sanitizing at safety rest areas, knowing how vital they are to the freight community. These efforts resulted in state safety rest area workers receiving the American Public Works Association excellence award.
A hiring freeze due to pandemic-related revenue decreases left WSDOT unable to hire summer temporary crews as well as fill open permanent positions. Mandatory furloughs beginning in July 2020 further restricted the amount and scope of work that could be accomplished. As a result, some time-specific work was not completed during these months. Roadside trash pickup and homeless encampment cleanups were also reduced as WSDOT had to prioritize emergency and safety-focused work first.
WSDOT Highway Maintenance—always answering the call
When the pandemic hit Washington, WSDOT safety rest area crews kept working in the field as essential workers to provide facilities for freight haulers, essential workers and other travelers. They increased the frequency of their cleaning to help keep travelers safe. This meant cleaning all 45 year-round state rest areas at least twice a day. At the most heavily used sites along I-5, I-90 and I-82, all touch points (door handles, faucets, handrails, etc.) were cleaned every two hours. Crews also worked repairing the rest areas to keep them open and in good working order.
The state chapter of the American Public Works Association honored this dedication with their "Empowering Teams Award," announced during their fall conference. Gov. Jay Inslee also recognized rest area crew contributions.
WSDOT uses Bailey bridges to keep traffic moving during projects
WSDOT bridge and maintenance crews recently helped place temporary Bailey bridges to keep traffic moving at two projects (State Route 21 Sanpoil Bridge replacement and Walla Walla County Seven Mile Bridge replacement). WSDOT has used the Bailey bridge system five times in the last nine years (2012-2020) compared to 10 times in the 52 years prior (1959-2011). The increased use of Bailey bridges is a good indicator of the need for preservation funding, as it is a result of aging infrastructure.
WSDOT State Route 21, Sanpoil Bridge replacement
A new bridge was needed after a major support on the West Branch Sanpoil Bridge partially washed out during extreme spring runoff flooding in April 2017. The bridge is located approximately 15 miles south of Republic in Ferry County.
Because the emergency funding needed to replace such bridges can take some time to arrive, a temporary Bailey bridge was put through the area. A new bridge was constructed and opened in fall 2020, and the Bailey bridge was then removed.
Walla Walla County, 7 Mile Road bridge replacement
When a county bridge over Mill Creek on 7 Mile Road in Walla Walla County was damaged by floods in 2020, WSDOT again assisted, helping to end more than eight months of travelers having to take a five-mile detour around the site. The detour was on a steep, gravel road that likely would have had to be closed during winter weather.
Floods eroded the foundation of one of the bridge's piers, making it unsafe for travel and leading to its closure in February 2020. In October, WSDOT installed an agency-owned Bailey bridge while the county continued its work on a permanent replacement.
The Bailey bridge is expected to be in place over Mill Creek until 2024, with construction of the replacement bridge starting in 2023.
Why Bailey bridges are important to WSDOT
Bailey bridges are portable, pre-fabricated truss bridges that do not require special tools or equipment to assemble and can be easily lifted and set in place, especially in areas without much room to maneuver large pieces of equipment. WSDOT keeps a supply of bridge pieces to construct Bailey bridges as needed, often using them for more than one Bailey bridge project over several years.
WSDOT uses its Bailey bridges to keep traffic moving after a bridge has failed or needs to be removed for replacement. Although they often require some restrictions on amount or weight of traffic, these temporary bridges allow most local travelers to avoid longer detours until a permanent replacement structure is built. Bailey bridges serve an emergency function, but their frequent use is also a symptom of a lack of preservation and maintenance funding.